
The World of Rapid Prototyping
By Terry Wohlers
Published in the Proceedings of the Fourth International Conference On Desktop Manufacturing, September 24-25, 1992, San Jose, California
Copyright 1992 by Wohlers Associates
​
Solid Ground Curing (SGC) by Cubital
Cubital America Inc. (Troy, Michigan) is a wholly-owned subsidiary of Cubital, Ltd. Two West German and two Israeli corporations jointly own Cubital, Ltd. of Herzlia, Israel. The Cubital unit, called the Solider 5600 Solid Ground Curing system weighs 4.5 tons and is complex. Yet the machine will simultaneously build as many parts as you can position in a 20" x 14" x 20" (508 mm x 356 mm x 508 mm) volume and maintains accuracy of 0.1 percent according to the company. The Solider system irradiates and solidifies a whole layer in a few seconds, regardless of size, complexity and number of parts. Therefore, processing speed may be an advantage of this system if you are making large or multiple parts.
The system charges a glass mask plate as it passes over an ion gun, which in turn shoots ions on the glass at a resolution of 300 dot per inch (118 dots per cm). This forms a pattern which is a negative image of the cross section. The system presents black electrostatic toner which adheres to the ion charged portions of the plate. The transparent areas reflect precisely the cross section of the part(s). The system positions the plate closely over the top of a thin layer of liquid polymer, and an intense flood of ultraviolet light shines through the plate, exposing the entire layer.
After being exposed to the light for a few seconds, the polymer solidifies and the system moves the partially finished part away from the exposing chamber. The solidified layer then undergoes several processes before the system produces a new layer. While these processes are underway, the system wipes the toner from the glass plate and processes the next cross section.
The system removes, by suction, the unhardened liquid surrounding the hardened layer. A thin layer of wax is then spread over the entire layer, filling the areas that before held liquid polymer. The wax, which goes through a cooling process, surrounds and supports the part. Finally, the partially finished part moves to a milling station. It mills the layer and produces a flat surface ready for the next layer. All of this repeats, automatically, until the part is complete. The surrounding wax must be melted away using hot tap water, a hot air gun, a microwave oven, or a conventional dish washer.
The system, priced at $490,000, constructs parts at a rate of about 1.5 cubic inches (28.1 cubic mm) per hour. Additionally, the process requires about 20 minutes of preprocessing time - from raw CAD file to the first layer built. The company has sold several systems in the U.S. and Europe.

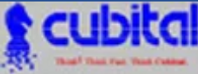
